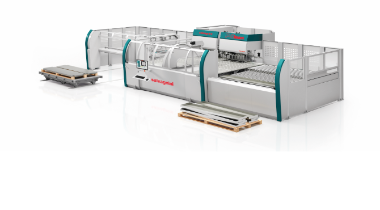
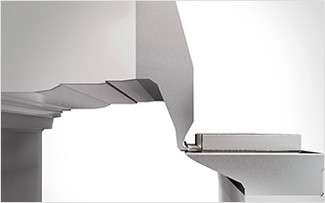
事例概要
業種 | 食品用機械 | 製品形状 | 食品機械カバー及び部品 |
板厚 | t0.4~t1.2 | 生産量 | 1個(オーダーメイド) |
課題 | パネルと部品を同時タイミングで生産すること、安全な加工環境への改善 |
導入背景
物件対応で流し生産(完全オーダーメイド生産)での板金加工をしていますが、
お客様ごとの発注ごとに設計された製品の加工を行っていました。
オーダーメイド品のため寸法が都度異なり、プレスブレーキの段取り替えの多さが問題となっていました。
これまでは対策としてワンタッチ金型等の装置を使用して段取り時間の短縮をしていました。
しかし、根本的な部分から改善をしたいと考えてパネルベンダーも含めて検討を始めました。
主に機械を覆うカバーパネルの加工と製品の部品の加工の2つに分かれますが、
パネルベンダーで加工すると、どうしてもパネルベンダーでの生産が早く、
従来パネルベンダーで加工出来ない製品の次工程への供給のタイミングが遅くなってしまう事がわかりました。
そこで、パネルベンダーのオプションで補強の様な「製品の幅が小さな製品」を加工し、切り離すカットオプションを選択しました。
パネルとその周辺の補強を同時に板金加工出来る為、次工程への部品供給もスムーズとなり、全行程時間の短縮ができました。
補強の加工は通常プレスブレーキで加工していましたが、稼働部分に製品を持った指を近づける必要があり、危険な作業でした。
幸い、これまで事故自体は怒っていませんでしたが、ヒヤリハットはたびたび発生しており、ここを改善しないといつか大きな事故につながってしまうと懸念していました。
補強加工は安全装置を使用しない板金加工が慣例でしたが、近年の法令改正により安全装置を使用して板金加工が必要となりました。
しかし、これまで1回の曲げ加工で必要な加工時間が4秒であったのに対し、安全装置使用すると7.5秒となり、生産数が少なくなる状況となっていました。
このままでは工場全体の生産性が落ちてしまうため、安全装置を使用しても生産性を上げる必要がありました。
導入効果
板金折り曲げ機械.comを運営しているサルバニーニジャパンとパネルベンダーを検討した結果、
製品ごとに異なる寸法へ約6秒で押さえ金型の長さを変更できて、これまで苦労してきた段取り替えを考慮することなく生産が出来ることがわかりました。
結果的に加工時間が60%削減出来ました。
加工時間が3分の1強に短縮された事で曲げ工程時間が短縮されたため、決められた時間の中での生産量が増えました。
またオプションで選択したカットを使用して補強も加工できるため、作業者のヒヤリハットを気にする事なく生産が可能となりました。
生産性を上げながら安全対策にもつながり、課題だった部分を解消できました。
パネルと部品の生産のタイミングを合わせる部分も、補強を加工出来るため次工程への同時搬入が可能となり、部品を探す手間も省けるようになりました。
抜き加工時のバラシ作業もカットオプションを使用すると必要なくなったため工程時間の短縮ができました。
バラシ作業は各工場で問題となっていましたが、工程時間には考慮されていないため対策がなかなか打てていませんでしたが、解決できてよかったです。
これまでプレスブレーキで危険な作業となっていた製品の加工は、可能な限りカットオプションを使用する事でヒヤリハットが無くなってきました。
危険な作業が無くなった事で作業者のストレスが少なくなり、工場自体も安全性を上げて曲げ加工できるようになりました。