今回は、サルバニーパネルベンダー3台、ファイバーレーザー、
パンチング・シャーリング複合マシンを持つスペインのJOBショップ(請負会社)の事例をご紹介いたします。
★動画は下記方法にて日本語字幕が利用できますので、ぜひご覧ください★
【動画を再生→動画の右下にある設定をクリック→字幕をクリック→ドイツ語か英語を選択→もう一度字幕をクリック→自動翻訳を選択すると言語一覧が表示されるので、下の方にある日本語を選択】
※もし字幕が出ない場合は、こちらの記事最後に和訳全文を掲載しておりますのでそちらをご覧ください
Teklanは1997年初めに設立されたスペインのJOBショップ(請負会社)です。
国内の請負会社でなんと唯一、パネルベンダーを3台所持するTeklanですが、
なぜそのような投資を決定したのでしょうか?
それでは早速、下記よりお読みください。
リーマンショックを乗り越えたTeklan社が直前に導入した機械
Teklanは現在3台のパネルベンダーを所有しており、
そのうちの1号機を購入・設置されたのは2008年8月のことでした。
その直後、リーマンショックによる世界的な経済危機が起きました。
ヨーロッパにおいても廃業倒産に追い込まれた会社が多かった中、
Teklanは市場に生き残るため受注に全力を注ぎ、機械を稼動させ続けました。
結果リーマンショックを乗り越えただけでなくビジネスを大きく成長させることができました。
そのような結果を得られたのは、
直前にパネルベンダーを導入できていたことが大きな要因の一つと言えます。
パネルベンダーがなければ、
リーマンショックを乗り越えることはできなかったかもしれません。
パネルベンダーによる2つの戦略
Teklanは全国で唯一、サルバニーニのパネルベンダーを3台持つJOBショップですが、
3台はそれぞれ異なる仕様となっており、
一番大きなものは長さ3495mm、高さ254mmまでの板金加工が可能です。
パネルベンダーと聞くと、基本的には大ロット向けで、
初めのパーツはセットアップのためスクラップになって無駄になる、
などと考えている人も多いかと思います。
パネルベンダーの他にもサルバニーニのレーザー、
パンチング・シャーリングマシンを導入しているTeklanですが、
パネルベンダーにおいては2つの全く異なる戦略で使用されています。
すなわち、大ロット生産の場合と、小ロット生産の場合です。
大ロットの場合、例えば2メートルの大きなパーツを生産する場合、
一人のオペレーターが積み重ねるなどの作業をしている間に、
機械が生産を開始できます。
そして第二の方法が小ロット生産の場合です。
例えば10個のパーツで構成される精巧な製品があったとします。
欧米のプレスブレーキでは生産するために10回金型を交換する必要があります。
しかし、サルバニーニのパネルベンダーは自動ブランクホルダーを備えており、
材料を次々と載せていくだけで自動的に金型構成を変更し調整することができます。
更に、MAC2.0技術により、
板厚や材質のデータベースと比較して材料のばらつきがあれば自動補正され、
曲げの品質が保証されます。
ステンレスの曲げ品質も非常に高く、
パーツの品質を維持するために重要な高価な保護フィルムも傷つけません。
そしてこれらのパネルベンダーでの作業において、
オペレーターはパーツの搬入出だけを行えばいいので、
非常に負担が少なく済みます。
このように、2つの戦略を持つことでパネルベンダーを最大限に有効活用することができます。
JOBショップがパネルベンダーを導入する必要性
TeklanはJOBショップなので、
投資となると自社製品を持つメーカーとはわけが違ってきます。
今後、どのようなパーツを製造していくのかが分からないので、
結果的に投資の判断がとても難しいのです。
それでも、私達は前に進むしかありません。
テクノロジーはどんどん進化していくのだから、
私達もそうしなければならない。
15年前の機械にこだわっているわけにはいかないのです。
今は、コンピューターによって図面がとても綺麗に描かれており、
私達はそれらを加工できる機械を持っていなければなりません。
サルバニーニの機械であれば、明らかにそれが可能なのです。
私達は、この機械が市場で強くあり続けるための助けになると確信しています。
私達は前に進み続けるしかありません。
15年前の機械にこだわっていてはだめなのです。
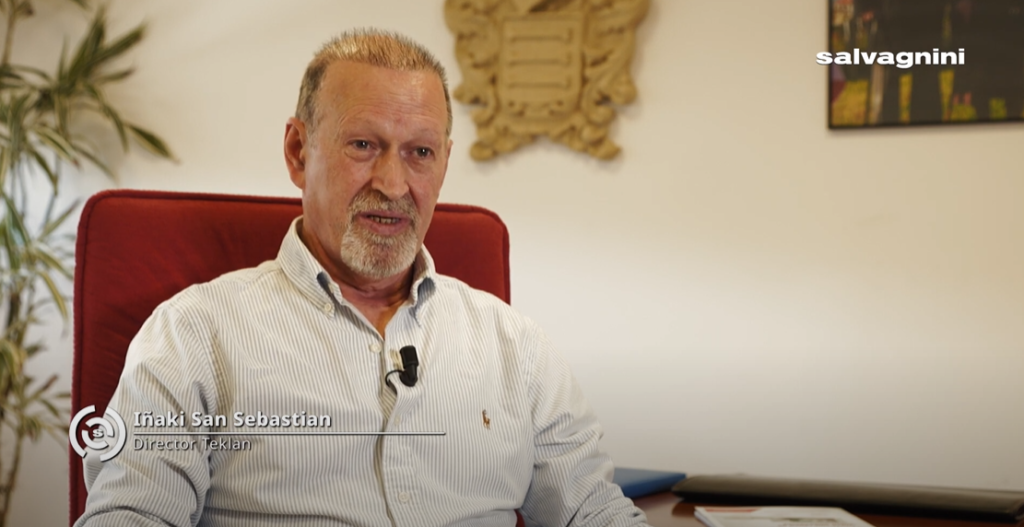
いかがでしたでしょうか?
リーマンショックという大きな経済危機を、
パネルベンダー導入していたことで乗り越えられたというお話は、
弊社としてもとても驚きで、またありがたいお話だと思いながらご紹介させて頂きました。
コロナ禍による経済悪化はリーマンショック以来、
かつリーマンショックをも超えたと言われていますが、
そんな今だからこそ、弊社のパネルベンダーがお役に立てるのではと考えます。
また、コロナ禍が収束したとしても、
気候変動問題が悪化し続けるなか、いつまた似たような状態に陥るかも分かりません。
ぜひこのコロナ禍のピンチをチャンスと捉えて、
パネルベンダーの導入を検討してみてはいかがでしょうか。
皆様からのお問合せ、いつでもお待ちしております!
インタビュー全文はこちら↓
テクランを設立したのは1997年の初めです。
当初はレーザーを導入し、パンチングを行うだけでしたので、少しずつチームを増強し、機械も買い足していきました。
2008年には、サルバニーニ社製のパネルベンダー1号機という重要な投資を行いました。
8月にパネルベンダーを設置した直後の9月に危機が訪れ、機械用の仕事を得るために市場で非常に活発に活動することを余儀なくされ、ビジネスが成長しました。
私たちは、全国で唯一、サルバニーニのパネルベンダーを3台持っている下請け会社です。
この3台はそれぞれ全く異なり、フル装備で、一番大きなものは長さ3495mm、高さ254mmまでの板金加工が可能です。
APC2技術を搭載したレーザーがあり、この機械は切断品質を調整しながら自動で動くので、非常に重要です。
切断品質が悪いとレーザーが停止するので、製造の無駄を省き、製造コストを抑えることができます。
また、パンチング・シャーリングマシンを導入したのは、私たちの生産構成では金型交換が多く、他のマシンではタレットを回したり、パンチを交換したりする必要があるためです。
他のメーカーの機械は、ストライカーが1つで、それが壊れると機械が止まってしまいます。
その代わり、私たちが購入したサルバニーニの機械には46本のストライカーがあります。
1本が故障しても、あと45本があります。
また、長さ500mmと一般的な76mmの仕上げパンチとは異なり、シャーが内蔵されているため、作業品質も向上しています。
機械だけでなく、製造工程にも多くの投資をしました。
機械は、人間の作業や適切なプロセスがなければ、100パーセントの効率を達成することはできないと悟ったからです。
よくパネルベンダーは大ロット用で、最初の部品は段取りでスクラップになってしまう、などと思われがちですが、そうではありません。
私は逆に、パネルベンダーは2つの全く異なる戦略で使うことができると考えています。
まず、当然のことながら、大ロットの場合。
例えば、2メートルの大きな部品であれば、一人のオペレーターが積み重ねなどの作業をしている間に、機械は生産を開始します。
しかし、パネルベンダーを解釈する第二の方法があります。
例えば、10個の部品で構成される精巧な製品があるとします。
従来のプレスブレーキでは、10回金型を交換する必要があります。
サルバニーニのパネルベンダーは、自動ブランクホルダーを備えており、材料を次々と載せていくだけで、自動的に構成を変えることができます。
さらに、MAC2.0技術により、厚みや品質のデータベースと比較して、材料のばらつきがあっても90度曲げることを保証します。
また、ステンレス部品の曲げ品質も非常に高く、部品の品質を維持するために重要な高価な保護フィルムも傷つけません。
パネルベンダーの作業では、オペレーターはパーツの出し入れをするだけなので負担が日以上に少ないです。
私たちは下請け業者なので、投資となると自社製品を持つのとはわけが違います。
今後、どのようなパーツを製造していくのかが分からないので、結果的に判断が難しいのです。
私たちは前に進むしかないのです。
技術はどんどん進化していくのだから、我々もそうしなければならない。
15年前の機械にこだわっているわけにはいかない。
今は、コンピューターによって、図面がとても美しく描かれています。そして、それを加工しなければなりません。
サルバニーニの機械は、明らかにそれが可能です。
私たちは、この機械が市場で強くなるための助けになると確信しています。