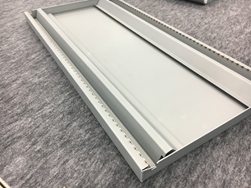
導入背景
オフィス家具用の側板などを加工製造していますが、カバーやBOXは強度と耐久性が必要なため、裏側に補強材が必要です。
これまではプレスブレーキで加工を行っていましたが、補強材はカバーやBOXの本体とは別に加工する必要があり、
補強材のために抜き、切断、曲げ加工を行っていました。
補強材のための別加工には工数がかかっており、
さらに補強材を溶接するための位置決めも必要であったため、加工工程を改善できないかと悩んでいました。
導入効果
パネルベンダーを使うことを前提として設計変更を行ったところ、製品と補強材をまとめて曲げることができるようになりました。
カバーやBOXといった製品の形状と補強材の形状を組み合わせることで一度の工程で曲げを行うことができるようになりました。
これまではプレスブレーキでの加工を前提とした設計だったため、これ以上の工程効率化、工程削減はできない状態でしたが、
パネルベンダーを前提として設計を少し変えるだけで曲げ加工を完全に自動化することができました。
これまで必要だった補強材の別加工が不要になったので、生産コストを削減できただけでなく、
一度に曲げを行うことで、補強材と製品を溶接する時の位置決めも不要となり、溶接工程も工数を削減できました。
パネルベンダーについて詳しくありませんでしたが、パネルベンダーを自社でどう使えば効率化するか、
サポートが充実していたので、本当に助かりました。