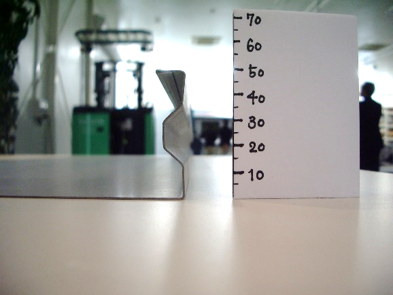
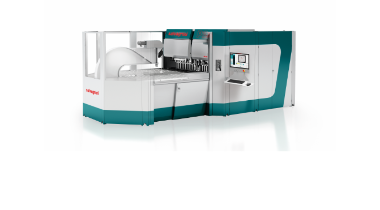
導入背景
関西で板金加工を受託しており、筐体の製作をメインで折り曲げ加工しています。
特殊形状(しぼり)を特殊金型を使ってプレスブレーキで加工していますが、どうしても品質が不安定でバラつきが発生し、板金加工できるオペレーターが限られてしまっていました。
加工できるオペレーターのうち一人の定年退職が迫っていて、これからしぼり形状の板金加工ができる職人が減ってしまうことが予想されているため、ますます融通が利きづらくなってしまうため困っていました。これからのために汎用機の板金機械で板金加工できるように工場を改善したいと考えており、更新を機に折り曲げの工程を改善できるような板金機械を探していました。
また、厚物の厚板加工のオペレーターの負担が大きいため、改善したいと考えていました。
板厚2.6㎜や3.2㎜の厚板加工も折り曲げており、最大サイズが1枚で20㎏弱ある板金の場合、オペレーターがコルセットを使用して作業しており、この作業環境を改善したいと考えていました。
導入効果
プレスブレーキではどうしても特型(特殊金型)を使用しなければいけないですが、パネルベンダーを活用して特型の加工を不要にすることができました。
また、パネルベンダーを活用することで1つ当たりの加工時間が半分以下抑えられ、板金加工の効率化ができました。
金型交換の手間がなくなったことも作業時間の短縮につながり、これまで“当たり前”と思っていた部分も大きく生産性をアップすることができました。
導入前はパネルベンダーを使いこなせるか少し不安でしたが、導入のサポートも充実しており、プレスブレーキ2台分の仕事をこなすことができるようになりました。
結果的に、これまでオペレーターが2名必要だった工程が1名でこなせるようになり、人手不足の中でも工場の効率を上げることができました。
もう1つ懸念であった厚板加工(厚物の板金加工)でのオペレータの作業環境改善について、パネルベンダーを活用した結果、オペレータが重量物を持つ回数を減らすことができました。材料を持つのは材料を機械にセットする際と、板金加工した後に製品を取り出す際の2つだけになり、作業環境を改善し、キツイ工程ではなくなりました。
さらに、その材料を持つ際は大物や厚物の材料を持ち上げる必要がなく、材料をスライドさせるだけなので肉体的な作業者への負担も大幅に軽減することができました。従業員からは腰痛が改善したという声があり、プレスブレーキからパネルベンダーへ変えて正解でした。