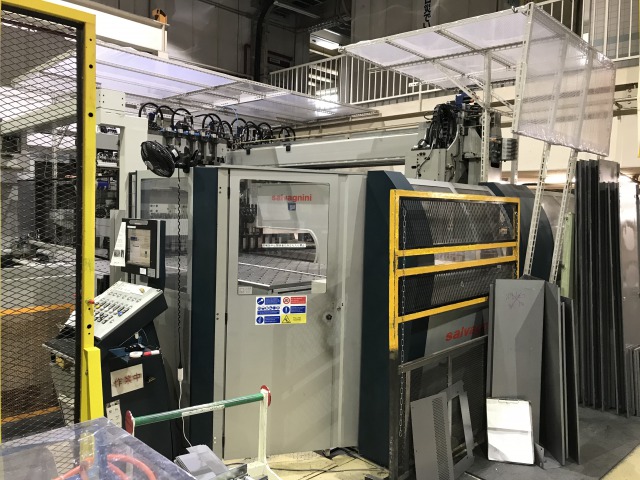
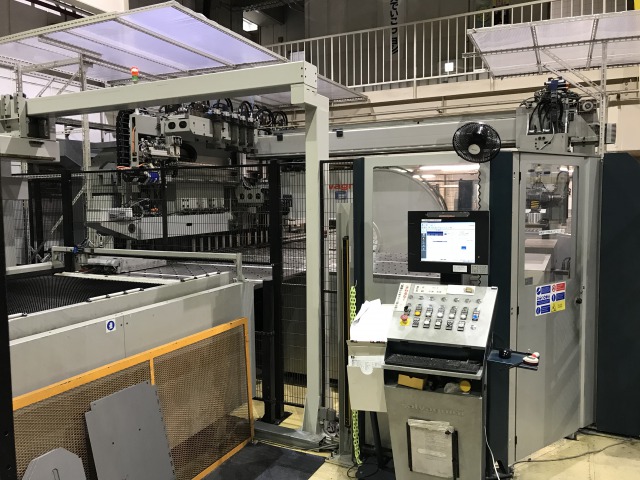
導入背景
中部地方で配電盤用の筐体、扉、パネル等の製造を行っている板金加工メーカーですが、工場の敷地が限られており、プレスブレーキを複数台設置して板金加工を行うことが難しい状況でした。板金加工する配電盤の素材は重量があり、重量物曲げとなるので作業者の負担が大きい状況でした。
プレスブレーキを使った折り曲げ加工では、重さ40~60kgある扉を、連続的に約20枚曲げる必要があり、作業者が腰を痛めてしまうことが多発していました。さらに、配電盤自体が-品-様であるため、筐体、扉、パネルなどの板金加工も多品種少量生産となり、生産効率のアップが難しい状況でした。
生産性を上げるために筐体t1.6パーツと扉t2.3パーツをキットごとに製造したいと考えていましたが、プレスブレーキの台数がかぎられているため金型交換が多発し、パーツごとの製造になってしまっていました。また、作業スペースが狭く、パーツごとの製造であっても置き場所に困ってしまい、作業者の負担を減らしつつ、生産性を上げる方法を検討していました。
導入効果
パネルベンダーを使うことで生産性を上げられないかと相談したところ、工場のスペースを有効活用する方法としてブランキング設備とパネルベンダーをライン化して、省スペースで効率の良い生産ができるようになることがわかりました。
実際に導入したところ、ブランキングからパネルベンダーでの曲げまで自動化されてライン生産になったため、作業者の負担を大幅に軽減することが出来た。結果的に、重量物をプレスブレーキで曲げる割合が約80%減少することができました。さらに、プレスブレーキで曲げ加工をしていた時に作業者の負担を軽減するために2名の増員を検討していましたが、パネルベンダーで自動化できたため採用する必要がなくなりました。
生産性を上げるために検討していたキットごとの製造についても、ブランク工程から曲げ工程までキットでのライン生産ができる様になりました。これまではパーツ探しやパーツを集める時間が約2時間/日ありましたが、0時間となり不要になりました。
生産性はキット生産によって全体的に生産効率を約2倍上げることが出来ただけでなく、以前はあとで使用するパーツが、工程内に散乱していた工場内がその都度用意することになったため、工場内の2Sが実現できました。