今回は、電動コンパクトパネルベンダーP1を導入したオーストリア企業の事例をご紹介いたします。
★動画は下記方法にて日本語字幕が利用できますので、ぜひご覧ください★
【動画を再生→動画の右下にある設定をクリック→字幕をクリック→ドイツ語か英語を選択→もう一度字幕をクリック→自動翻訳を選択すると言語一覧が表示されるので、下の方にある日本語を選択】
※もし字幕が出ない場合は、こちらの記事最後に和訳全文を掲載しておりますのでそちらをご覧ください
今回ご紹介するのはAKE社へパネルベンダー「サルバニーニP1」を導入した事例です。
同社は1998年に設立されたIDEALの姉妹会社で、ファストフード業界、特にサービスエリア向けのディスプレイケースを専門にしています。主にヨーロッパ市場を中心に海外にも展開しています。
サルバニーニシステムを導入する前は従来のプレスブレーキを使っていましたが、いくつかの複雑な形状には熟練の技術者による加工が必要不可欠であり、そのような技術者が慢性的に不足している状況に悩んでいました。
そこでサルバニーニP1を導入したところ、
処理工程が削減できたことで加工時間がわずか4分の1になり、
また熟練した技術者でなくても、誰でも複雑な形状が同じようにでき、1-1000個のバッチを生産できるようになりました。
導入背景
1998年に設立されたIDEALの姉妹会社で、ファストフード業界、特にサービスエリア向けのディスプレイケースを専門にしているAKE社。
同社は顧客の要望に応じてオーダーメイドのディスプレイを生産しており、現場への設置を含めておよそ3-4週間で納品しています。
主にヨーロッパ市場を中心に海外にも展開しており、現在AKE社は240名の従業員、IDEAL社は220名の従業員を擁しています。
そんなAKE社ですが、サルバニーニシステムを導入する前は従来のプレスブレーキで曲げ加工を行っていました。
プレスブレーキで曲げ加工をする場合、熟練工でないと形状が出せないほど複雑なものも中にはありましたが、オーストリアでは他の国・地域と同様に熟練した技術者が慢性的に不足していたことから、人材の確保に頭を悩ませていました。
この技術者不足を解消して複雑な形状でも安定的に加工できる体制を構築したいと思ったことが、自動化とサルバニーニに興味を持った理由でした。
導入効果
P1で実現した最大のメリットは加工工程の削減であり、その最たる例がディスプレイサンプ(水溜め)の加工です。
AKE社のすべてのディスプレイにはこのディスプレイサンプを使用していますが、従来のプレスブレーキでこの加工を行うには非常に複雑な形状であり、加工に多くの時間がかかっていました。
そこでパネルベンダー「サルバニーニP1」を導入したところ、加工時間をわずか4分の1に削減できました。
また、P1のもう一つの利点は、熟練の技術者でなくても、一定の教育を受けたスタッフであれば誰でも同じように機械を使用できることで、これにより1-1000個のバッチを生産できるようになったことです。
最後に三つ目の大きな利点は、高い繰り返し精度を実現できたことです。
同社の生産にはロボットによる下流のレーザー溶接工程が含まれており、これが生産の鍵を握る重要な工程となっています。
そこにP1の持つ高い繰り返し精度という技術を手にしたおかげで、材料の節約と加工効率の向上を図りながら、最終的には設計自体の見直しを行うことができました。
数年後には、2台目のP1、P2が必ずAKEに設置されることでしょう!
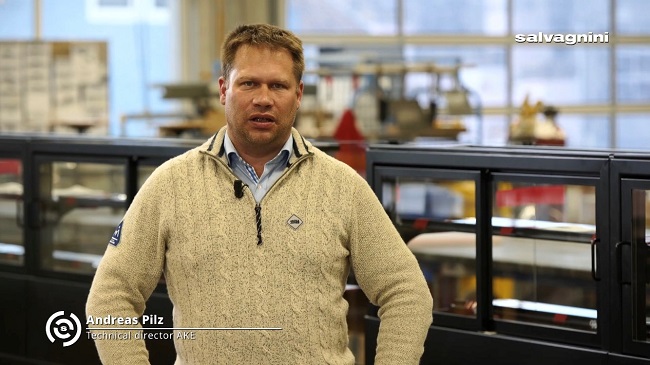
インタビュー全文はこちら↓
AKEは1998年に設立された会社で、IDEALの姉妹会社です。
現在、AKEは240名の従業員、IDEALは220名の従業員を擁しています。
AKE社はファストフード業界、特にサービスエリア向けのディスプレイケースを専門としており、主にヨーロッパを中心に海外にも展開しています。
お客様のご要望に応じて、1台、100台、1000台のディスプレイをオーダーメイドで製作し、必要に応じて現場に合わせた設置を含めて3~4週間で納品します。
私達はすべての私達の薄板金の生産を社内で製造します。
年間約2500トンのステンレス鋼を加工しています。ステンレス鋼のみを使用し、パンチレーザーコンビマシン、伝統的なプレスブレーキ、そして最後に最新のサルヴァニーニパネルベンダーを使用して、3交代で加工しています。
以前は、従来のプレスブレーキで板金を曲げていました。
残念ながら、いくつかの複雑な形状に必要とされる難しい作業を考えると、これは熟練した労働者を必要とし、オーストリアでは、他のヨーロッパの他の地域と同様に、熟練した労働者が慢性的に不足しています。
これが、我々が自動化とサルヴァニーニについて考え始めた理由です。
パネルベンダーを発見したとき、私たちはエンズドルフのサルヴァニーニを訪れ、P1とP2leanでいくつかのテストを行い、2つのうち小さい方を選択しました。
P1で実現した最大のメリットは、処理工程の削減であり、その最たる例がディスプレイサンプ(水溜め)です。
これらのサンプは、当社のすべてのディスプレイに使用されていますが、従来のプレスブレーキで製造するには非常に複雑です。
サルバニーニP1では、1つ1つにかかる時間がわずか4分の1になりました。
明らかに、P1のもう一つの利点は、訓練を受けたスタッフや補助スタッフが同じように使用でき、1-1000個のバッチを生産できることです。
私たちはオフラインでプログラムを設計し、機械上でバーコードを呼び出します。
サルバニーニ社との関係は、サービスの面でも販売の面でも非常に良好です。
もう一つの大きな利点は、繰り返し精度です。
当社の生産には、ロボットによる下流のレーザー溶接工程が含まれています。
最終的には、この技術により、材料の節約と作業効率の向上を図りながら、設計を見直すことができるようになりました。
数年後には、2台目のP1、P2が必ずAKEに設置されることでしょう。