プレスブレーキは100年以上前から存在しており、多くの製造業で愛用されていますが、パネルベンダーはGuido Salvagniniによって発明され、1977年に登場しました。
この2つの板金機械はそれぞれ、製造プロセスにおいて確固たる地位を築いており、独自の利点があります。
この記事を読んでいる人はプレスブレーキに精通している人でしょうから、
- パネルベンダーとは
- パネルベンダーとプレスブレーキとの違い
- どちらを選ぶべきか
をこの記事では紹介します。
目次
パネルベンダーとは
生産ラインの板金加工で最初に思い浮かぶのは「プレスブレーキ」ではないでしょうか?
プレスブレーキは、板金を最終的な部品の形状に折り曲げる主な方法ですが、一部の先進的な製造業者は、板金を成形するための有効な方法があることに気が付き始めています。
それは板金の折り曲げ機械、すなわちパネルベンダーです。
一般にパネルベンダーとして知られているこの機械は、従来のプレスブレーキと同じ形状の部品を製造できますが、一部の板金成形においてはプレスブレーキをはるかに凌ぐ生産性を誇ります。
それは、「すべての成形に標準工具を使用する」という点です。
パネルベンダーは、水平方向にフランジを形成する一対のブレードを備え、ブランクホルダー(1)が板金を安定して保持します。
この設計により、プレスブレーキではその都度特別な工具を必要とする曲げ加工において、パネルベンダーは仕掛り時間ゼロの効率性を発揮します。
パネルベンダーとプレスブレーキの違い
パネルベンダーとプレスブレーキの違いは、端的に以下のように表すことができます。
パネルベンダー | 薄い板金に適している。 速さと正確さを重視し、板金を傷つけずに曲げることが可能 |
---|---|
プレスブレーキ | 重くて厚い金属板に適している。 「曲げる」ことに重点が置かれている。 |
曲げ加工での比較

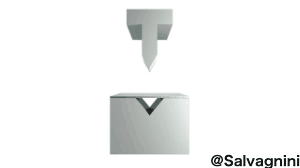
1:加工するオス金型(パンチ)による加圧
2:メス型(ダイ)でシートを固定

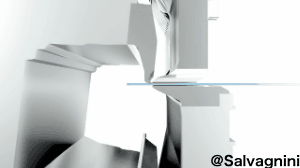
1:押さえ金型でシートを固定
2:円弧を描く曲げ刃による加圧
プレスブレーキには、少なくとも1人のオペレーターが常駐している必要があります。
対してパネルベンダーは、ほぼすべての成形プロセスでオペレーターを必要としません。
また、パネルベンダーでは曲げ加工は正曲げ、逆曲げ(ヘミング加工や R曲げを含む)を自動で行うため、訓練を受けていないオペレーターでも機械を使用でき、作業者の熟練度に加工精度や速度が左右されることはありません。
パネルベンダーを使うと、より早く、大幅に少ない人数で、より省コストに、より高い精度で、必要な時に製造できます。
段取りでの比較
パネルベンダーでは加工スタートまでの多くの工程を省くことができます。
また、曲げ形状による金型交換が不要で、金型長も自動で調整されます。
その為、多品種少量生産に効率よく対応することが出来ます。
プレスブレーキでは、金型の交換などセットアップの時間が発生します。
パネルベンダーは、セットアップ時間を事実上ゼロにすることが可能です。
パネルベンダーではほとんどの段取り時間が不要になります
位置決めの比較
パネルベンダーはプログラムに基づき位置決めピンが配置され、自動または手動(機種により異なります)でシートの形状に合わせ位置決めします。
自動で加工が行われるため、オペレーターの熟練度に製品の精度や加工速度が左右されることはありません。
また、パネルベンダーは位置決め時にシートの寸法を測定し、供給されたシートがプログラムされているものと異なればエラーが表示されます。
人間工学に基づいた位置決め
工具摩耗の比較
プレスブレーキでは、
- ツールは時々交換する必要がある
- 曲げ結果の段階的な劣化が発生する
- プログラムを再調整する必要がある
などの課題がありますが、パネルベンダーでは
- ツールの摩耗なし
- 低メンテナンスコスト
- 長年の使用後でも精密さを維持
といったメリットがあります。
どちらを選ぶべきか
プレスブレーキは、パネルベンダーと比較してかなり安価です。
対してパネルベンダーは、1時間あたりの板金成形効率ではプレスブレーキを大きく凌駕しています。
プレスブレーキ | パネルベンダー | 生産効率 | |
---|---|---|---|
機種/仕様 | B2-170T | P4-2116 HPT | – |
パーツA 加工時間 | 3分30秒 | 48秒 | 77%向上 |
パーツA 消費電力 | 0.46kW/h | 0.08kW/h | 83%向上 |
パーツB 加工時間 | 4分45秒 | 1分12秒 | 75%向上 |
パーツB 消費電力 | 0.63kW/h | 0.12kW/h | 81%向上 |
ロット生産 10set | 91分30秒 | 20分10秒 | 78%向上 |
ロット生産50セット | 420分 | 100分 | 76%向上 |
お客様から常に聞かれるのは、「プレスブレーキのセットアップ時間を最小限に抑える、あるいはゼロにする方法はないか」というものです。
誰もがセットアップ時間を短縮するために、プレスブレーキに自動化機能を追加しようと考えますが、最終的には、パネルベンダーが現実的な代替品となるくらいの費用が発生します。
暖房、換気、および空調、キャビネットなど、箱型の板金加工を行う製造現場では、パネルベンダーが最適なソリューションとみなすことができます。
完全自動化、半自動化、主導のどちらの機械を選択するかは、現場が追求しているワークフローと価格の折り合いによります。
まとめ
プレスブレーキは、板金曲げの主力製品です。
用途が広く、ツールが比較的安価で、操作が簡単です。
しかしその一方で、「自動化が難しい」という課題を抱えています。
私たちのお客様の1人は、設備の整ったプレスブレーキを200,000ドルで購入するか、パネルベンダーを4倍近い価格で購入するかを悩んでいました。
実際の現場調査したところ、同社のプレスブレーキ13台で1時間あたり平均8個の生産量であったのに対し、パネルベンダーでは1時間あたり60個と、ほぼ8倍の生産性がありました。
生産性とコストパフォーマンスの面で合理的に考えると、プレスブレーキがパネルベンダーに勝ることは難しいでしょう。
ただし、万能な工作機械であるプレスブレーキが無くなることはありません。
プレスブレーキで形成できないものはほとんどありませんが、パネルベンダーは材料の厚さ、ワークピースの長さ、フランジの高さなどの制約があります。
一方で、成形の精度、再現性、セットアップのしやすさという観点では、プレスブレーキではうまく機能しません。
おそらく、パネルベンダーの価格で、いくつかのプレスブレーキと小さなレーザーを購入できるでしょう。
しかし、パネルベンダーの生産性と投資対効果の数値をきちんと見れば、パネルベンダーもきっとあなたの選択肢のひとつに入ることでしょう。
関連記事