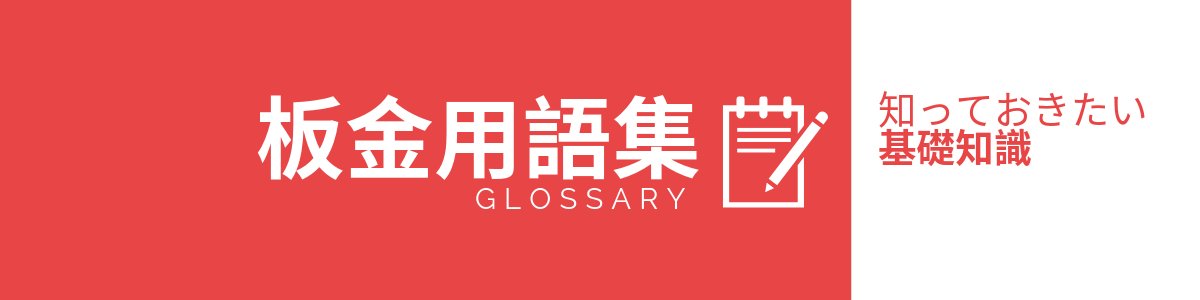
板金業界の折り曲げで知っておきたい用語集をご紹介します。
今さら聞けない基礎知識から新人教育にもご活用ください。
板金加工業界の折り曲げ機械で意外と知らない用語もご紹介しています。
板金加工に特化した最大級の情報サイト、パネルベンダー.comでは、用語だけでなく
日本全国の様々な事例、板金加工ノウハウをご紹介しています。
プレスブレーキは、薄いステンレス・アルミ板などを曲げ加工する際に使用されます。加工の仕組みとしては、機械フレーム下部に固定された型(ダイ)に、昇降する型(パンチ)を押し込むことで、薄い板を曲げています。この際、応力は曲げ中心部に発生しています。このプレスブレーキには、機械式と油圧式があります。機械式は、クランクを用いて昇降する型を動かすことで加工を行いますが、油圧式は、油圧シリンダーを用いてクランク(昇降する型)を動かし、加工を行います。一般的には加工精度に勝り、調節がしやすい油圧式プレスブレーキの方が、主流となっています。
パネルベンダーは、プレスブレーキとは異なり、素材の上下をブランクホルダーで固定し、上下に動く曲げブレードで側面から曲げを行います。このため、応力は側面に発生します。手動で加工する板を移動させなければならないプレスブレーキとは異なり、パネルベンダーは、自動で素材の曲げ部分を素早く正確に、プレスの前まで移動させます。そして、ブランクホルダー部が素材をしっかりと掴み、ブレードで高速且つ連続的に上曲げまたは下曲げを行うことができるため、素早い加工が可能です。そのため、一工程当たりにかかる時間とコストを抑えることが可能です。また、パネルベンダーは、プレスブレーキに対して自動で行われる作業が多く、作業者に依存する工程が少ない為、一定の品質を実現することが出来ます。
万能曲げツールは、板金機械の上刃や下刃に備わっており、パネルに合わせて、自動調整することで様々な形状のパネルに対応することが可能です。折り曲げ加工を行う際の、面倒なセットアップが不要なため、効率的かつ素早く曲げ加工を行うことが出来ます。またセットアップの際の時間が削減され、生産性が向上します。さらに、セットアップの作業が不要になるため、作業者の安全を確保する事にもつながっています。
ヘミング曲げは曲げ加工の一種で、金属の板を180度折り返す曲げ加工です。ヘミング曲げは、他にもあざ折りとも呼ばれます。ヘミング曲げ加工を行うメリットとして、金属の板の端部の強度を上げられることや、安全性の確保が出来ることがあります。特に、金属の板が薄い場合は板の端面が鋭利になるために、使用時に触れた場合には思わぬ怪我をする場合があります。そのため、ヘミング曲げ加工を行って内側に折り返すことで、板厚が増え、端部が丸くなるため、怪我のリスクを低減することが可能です。また、端面にヘミング曲げを行うことで、板厚が二倍になるため、端面の強度確保にもつながります。
レーザー加工機とは、レーザーを用いて様々な加工を行う機械です。レーザーを用いる加工は、刃物などを用いる加工と比べて、刃こぼれが発生しない点や、切断する部品に直接接触しないため、変形を防げる点、刃物を用いた加工に比べて微細な加工が可能な点等、様々なメリットがあります。一方で、ランニングコストや、導入コストが高いというデメリットもあります。
Z曲げは曲げ加工の一種です。Z曲げは、一回の曲げ加工と二回曲げ加工を行う場合があり、板厚によって異なります。例えば、板厚が垂直部分の数倍以下(5倍が目安)の場合は、一回の曲げ加工で成形できますが、板厚が垂直部分よりも数倍以上(5倍以上)の板を一回の曲げ加工でZ形状を成形しようとすると、割れが発生してしまう場合があります。そのため、厚めの板に対してZ曲げを行う場合は、注意が必要です。Z曲げを二回の曲げ加工にて行う場合にも、いくつか方法があり、L曲げを2回行う場合や、一度V曲げを行った後に、L曲げを行うことで、Z形状にするという方法などがあります。その際、位置決めにブレが生じることがありますので、十分注意しましょう。
V曲げとは、曲げ加工の一種です。90度を基本に、V字型の金型を用いて、金属の板などを曲げ加工します。V曲げにはいくつか方法があり、パーシャルベンディング、ボトミング、コイニングという方法があります。パーシャルベンディングとは、加工する金属部品などを部分的に金型に接触させて曲げを行います。この方法はV字部分の角度を自由に設定できる一方、一般的に技術難易度が高く、角度のバラつきが発生することがあります。一方でボトミングは、加工する金属部品を金型に押しつけることで加工を行います。この方法は精度が高い一方、曲げ加工時に元の形状に戻ろうとする「スプリングバック」が発生する為、それを考慮に入れて加工を行う必要があります。また、コイニングはパンチを食い込ませることで加工を行います。この方法も高い精度を実現できる一方で、成形に大きな力を必要とします。